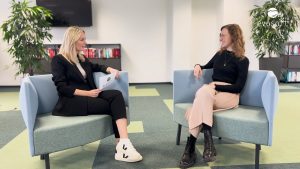
Inside evosoft: Der Jubiläums-Video-Podcast – Folge 2
evosoft feiert 30 Jahre Innovation, Teamgeist und persönliche Entwicklung. In der zweiten Folge unseres Jubiläums-Video-Podcasts erzählt Laura Willer, wie sie von einer Werkstudentin zur Technical Consultant